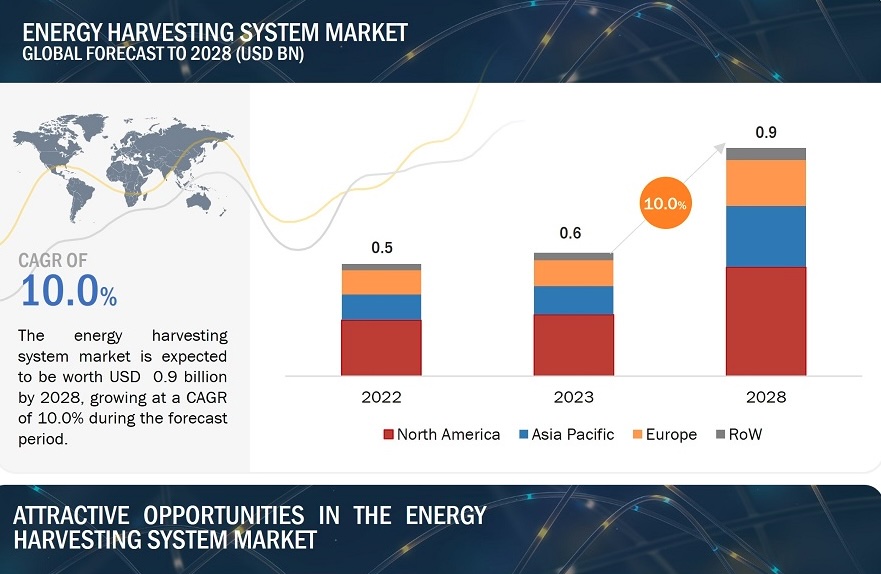
Energy harvesting accounts for the largest market share of the global smart textiles market by functionality, according to a recent report by Impactful Insights. The report puts the value of the smart textile market at $4.1 billion in 2023, and anticipates its rise to $24.5 billion in 2032, indicating a insignificant CAGR of 21.5 percent. In a separate report from Markets and Markets, the global energy harvesting market size itself was valued at $0.6 billion in 2023, and is expected to reach $0.9 billion by 2028, showing a CAGR of 10 percent over this period.
No single factor is driving this. Rather, a combination of government legislation, evidenced in funding policies and reflected in research and development (R&D), and paired with technology advances, miniaturization, design, sector and consumer demand, all contribute. This sector is still at a relatively early stage, but it’s growing rapidly in terms of advances and market. The time has come to look more closely at innovations in fiber development and textile energy harvesting, and to examine their importance.
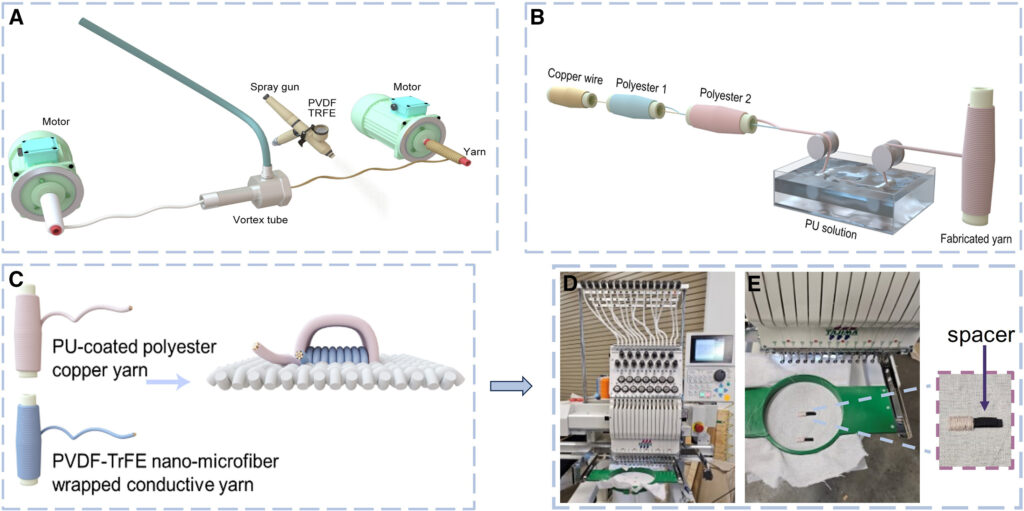
A design issue
Rong Yin is an Assistant Professor at North Carolina State University (NC State) with research on wearable electronics, including embroidering energy harvesting yarns for sensing functions. Professor Yin sees a clear benefit in embroidering yarns directly onto the textile. “During fabric production, you don’t need to consider anything about the wearable devices,” he explains. “You can integrate the power-generating yarns after the clothing item has been made.” The results are positive generating electrical signals that can be used as sensors on clothing and footwear.
“When we put the embroidery in a shoe, if you are running, it generates a higher voltage than if you were just walking,” he says. “When we stitched numbers into fabric, and press them, it generates a different voltage for each number. It could be used as an interface.”
So far so good, but there are still obstacles to be overcome before seeing a larger uptake in wearables. Part of this is the full-scale commercialization of the energy-harvesting yarns, but another issue, not raised often enough—or early enough—in the process, is design.
In a recent paper titled “A clickable embroidered triboelectric sensor for smart fabric,” published in Device Journal, Prof. Yin and colleagues identify an important design problem: “Most flexible electronic devices often still differ from traditional textiles in structure and construction, hindering their integration and scalability.”
As the paper title suggests, the researchers have used embroidery to demonstrate the potential of early design input, using an embroidery-based device to transform a conventional textile into a “clickable” button. This is done using an embroidery pattern with dual triboelectric yarns to enable a 3D structure. Optimization and customization are achieved by adjusting the spaces between the yarns needed for the triboelectric output, as well as other performance metrics, such as consistent contact and separation that are required for the clicking mechanism’s reliability.
In designing a 3D rather than 2D embroidery the researchers have found that both the triboelectrical output and tactile sensation are optimized by retaining a degree of separation between the top and bottom with different embroidery stitches used for each layer. A dual-sensor device has been created by combining two embroidered sensors with different gap sizes to allow for more complex inputs, and in being self-powering, there is an ease of integration with an imperceptible presence in the finished garment for the wearer.
Engineering flexibility
The effort to achieve performance, lightness, flexibility and wearer comfort in power supply for wearables is leading to the development of engineered fibers. Researchers at the University of Southampton in the U.K. and the Rajamangala University of Technology in Thailand are developing the use of hollow structure polymers for the purpose.
A one-step process is achieved using electrospinning to produce a hollow Polyvinylidene fluoride (PVDF) fiber with a diameter of around two microns. The use of a self-powered sensor eliminates the need for a separate battery, reducing weight and bulk to create greater flexibility in the garment and better comfort.
Military personnel and outdoor pursuit enthusiasts, in particular, may benefit, with energy captured from mechanical movement, such as is generated through foot, knee, hip and elbow movement, shown to be an effective source for conversion to electrical energy. In the engineering of the piezoelectric polymer, researchers are confident that it can be produced easily in a form that is both flexible and breathable, attributes particularly needed in wearables.
French chemical company Arkema has developed electroactive copolymers P(VDF-TrFE) with piezoelectric properties in a number of forms from powder to inks and films. Its Piezotech® FC can be processed into a coaxial fiber that has great potential for wearables, where it can be used for energy harvesting and sensing. The development sandwiches a piezoelectric layer between a center core and an outer layer that is conductive.
A number of different manufacturing processes can be used to produce the fiber. In one, an extrusion process is used directly on the core fiber, while another uses a coating, and a third process sees stripes of the copolymers wrapped around the central core. The Piezotech FC fiber has been found to have a high piezoelectric response over a wide range of temperatures in their poled ferroelectric phase, with high thermal stability of the piezoelectric properties. They also exhibit good mechanical properties, a high coupling factor, wide frequency range, transparency, chemical resistance and a high dielectric strength.
“The only limit is our imagination,” according to Fabrice Domingues Dos Santos, head of development at Piezotech. “One of the major innovations is that they generate their own energy from vibrations or ambient heat. These polymers bring a great deal of subtlety to applications such as haptic actuators in smart gloves, which can give the user the illusion of touching stone or velvet. This represents major progress compared with classic actuators—which vibrate like crazy!”
Dr. Marie O’Mahony is an industry consultant, author and academic. A frequent contributor to Textile Technology Source, she lives in London.